Методы нанесения фоторезиста обычно делятся на покрытие центрифугированием, покрытие погружением и покрытие валиком, среди которых наиболее часто используется покрытие центрифугированием. При нанесении методом центрифугирования на подложку капают фоторезист, и подложку можно вращать с высокой скоростью для получения пленки фоторезиста. После этого можно получить твердую пленку, нагревая ее на горячей плитке. Центрифугирование подходит для покрытия от ультратонких пленок (около 20 нм) до толстых пленок около 100 мкм. Его характеристиками являются хорошая однородность, равномерная толщина пленки между пластинами, небольшое количество дефектов и т. д., что позволяет получить пленку с высокими характеристиками покрытия.
Процесс центрифугирования
Во время центрифугирования основная скорость вращения подложки определяет толщину пленки фоторезиста. Зависимость между скоростью вращения и толщиной пленки следующая:
Спин=кТн
В формуле Spin — скорость вращения; Т – толщина пленки; k и n — константы.
Факторы, влияющие на процесс центрифугирования
Хотя толщина пленки определяется основной скоростью вращения, она также зависит от комнатной температуры, влажности, вязкости фоторезиста и типа фоторезиста. Сравнение кривых различных типов фоторезистивных покрытий показано на рисунке 1.
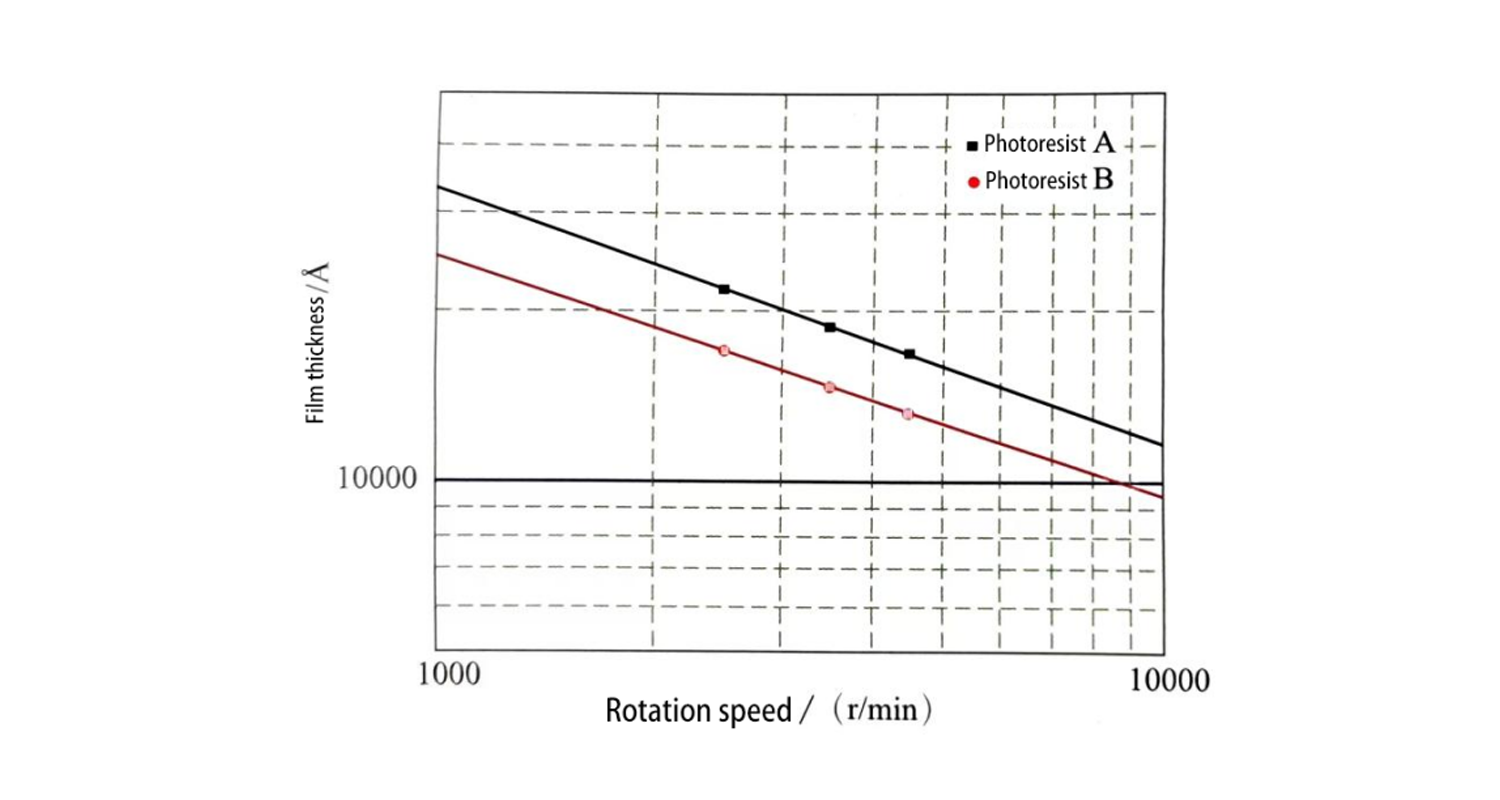
Рисунок 1. Сравнение кривых различных типов фоторезистивных покрытий.
Влияние времени основного вращения
Чем короче время основного вращения, тем больше толщина пленки. При увеличении основного времени вращения пленка становится тоньше. Когда оно превышает 20 с, толщина пленки практически не изменяется. Поэтому время основного вращения обычно выбирают более 20 секунд. Зависимость времени основного вращения от толщины пленки показана на рисунке 2.
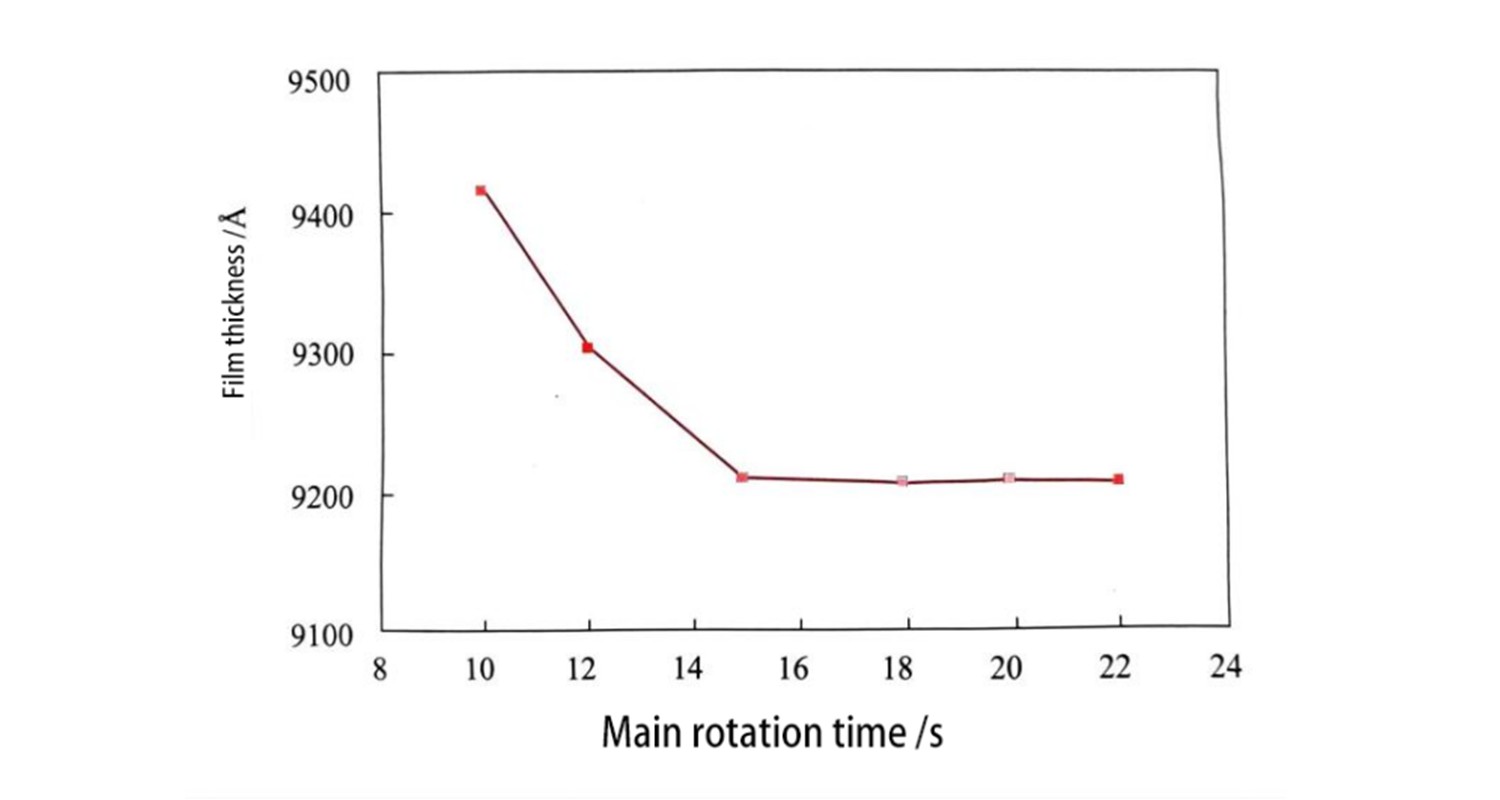
Рисунок 2. Зависимость между временем основного вращения и толщиной пленки.
Когда фоторезист капает на подложку, даже если последующая основная скорость вращения одинакова, скорость вращения подложки во время капания будет влиять на конечную толщину пленки. Толщина пленки фоторезиста увеличивается с увеличением скорости вращения подложки при капании, что обусловлено влиянием испарения растворителя при разворачивании фоторезиста после капания. На рис. 3 представлена зависимость толщины пленки от основной скорости вращения при различных скоростях вращения подложки при капании фоторезиста. Из рисунка видно, что с увеличением скорости вращения капающей подложки толщина пленки меняется быстрее, причем разница более заметна на участке с меньшей основной скоростью вращения.
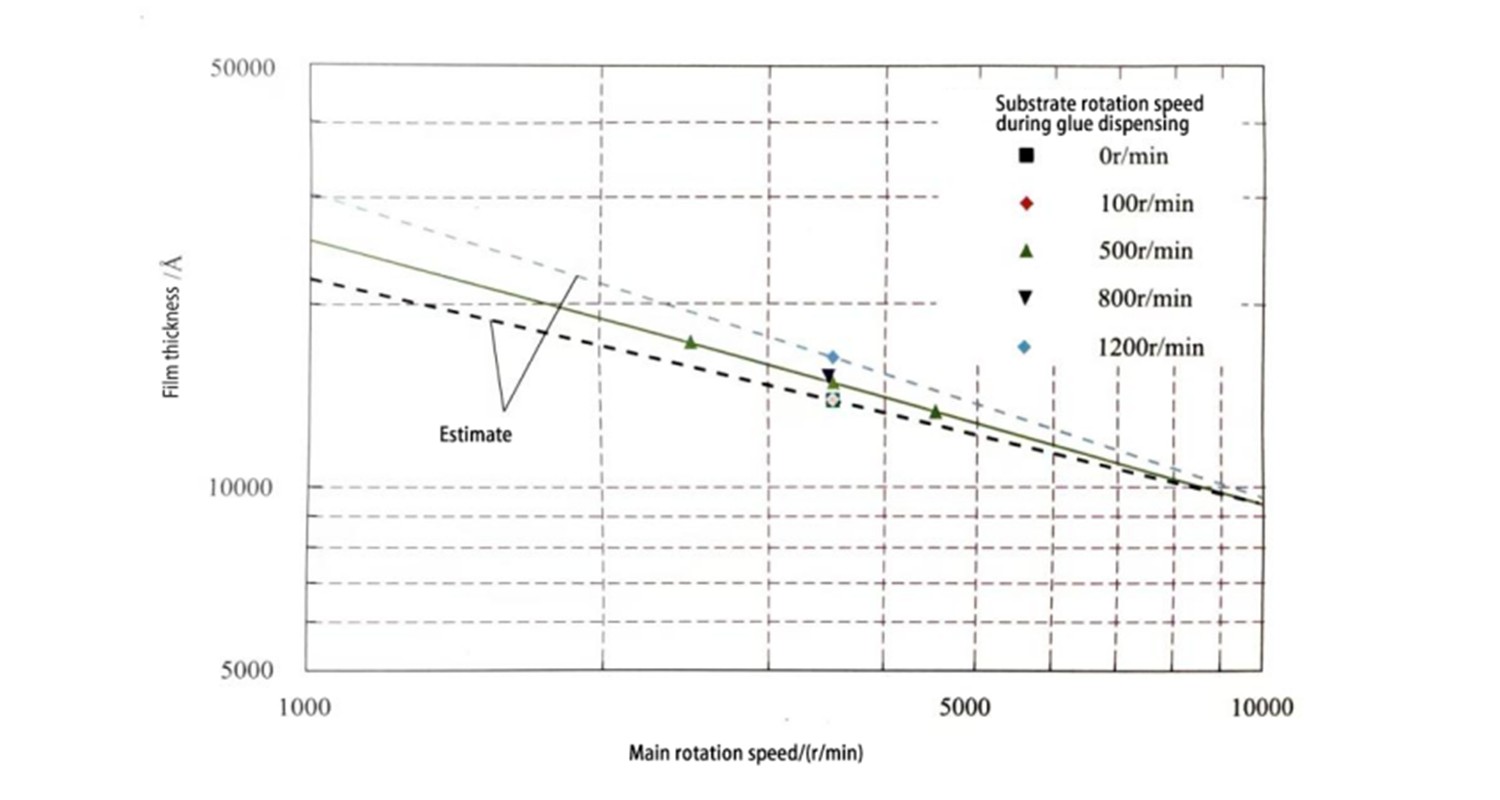
Рисунок 3. Зависимость между толщиной пленки и основной скоростью вращения при различных скоростях вращения подложки во время нанесения фоторезиста.
Влияние влажности во время нанесения покрытия
При уменьшении влажности толщина пленки увеличивается, поскольку уменьшение влажности способствует испарению растворителя. Однако распределение толщины пленки существенно не меняется. На рисунке 4 показана взаимосвязь между влажностью и распределением толщины пленки во время нанесения покрытия.
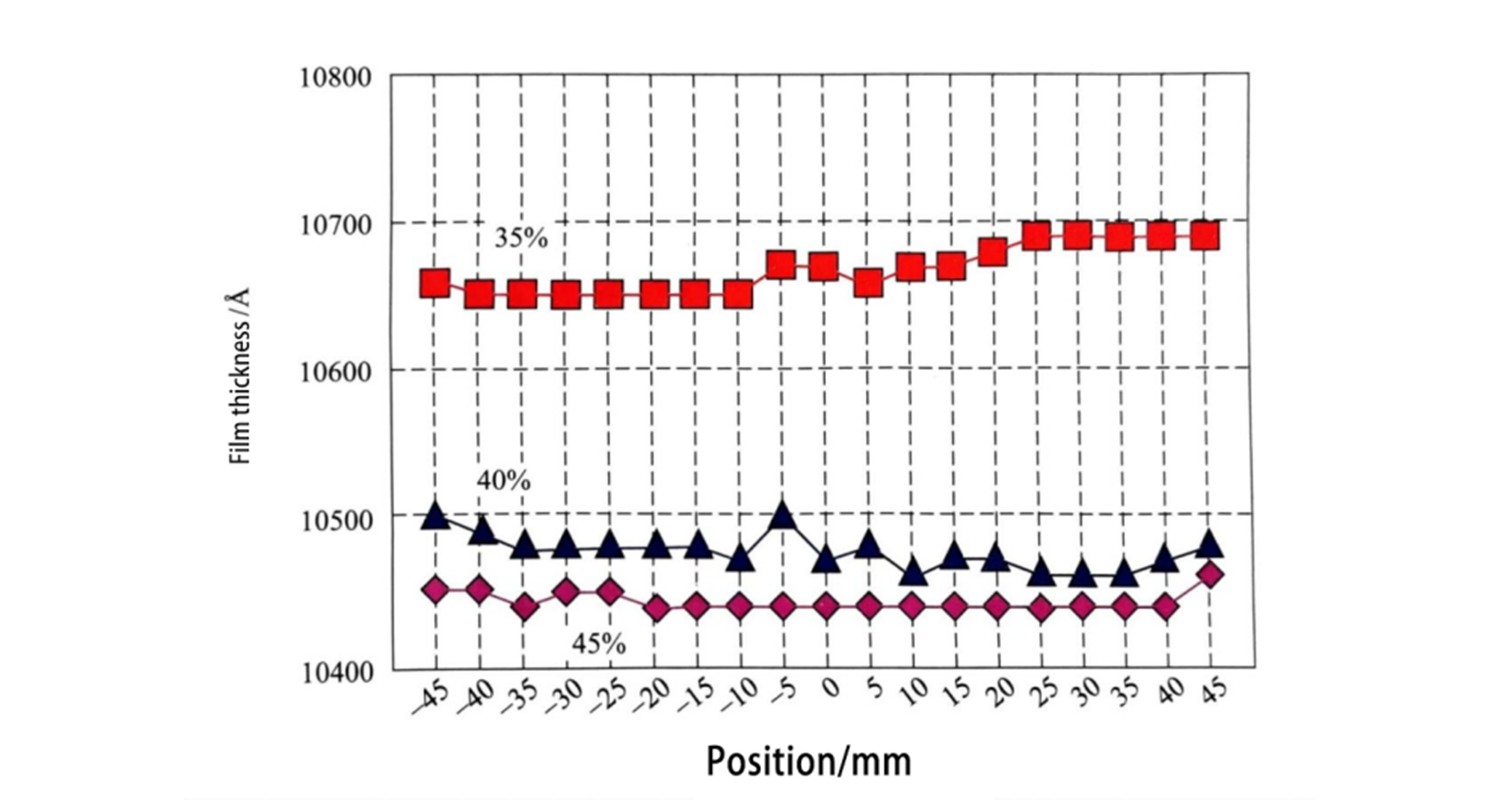
Рисунок 4: Зависимость между влажностью и распределением толщины пленки во время нанесения покрытия.
Влияние температуры во время нанесения покрытия
При повышении температуры в помещении толщина пленки увеличивается. Из рисунка 5 видно, что распределение толщины пленки фоторезиста меняется с выпуклого на вогнутое. Кривая на рисунке также показывает, что наибольшая однородность достигается при температуре в помещении 26°C и температуре фоторезиста 21°C.
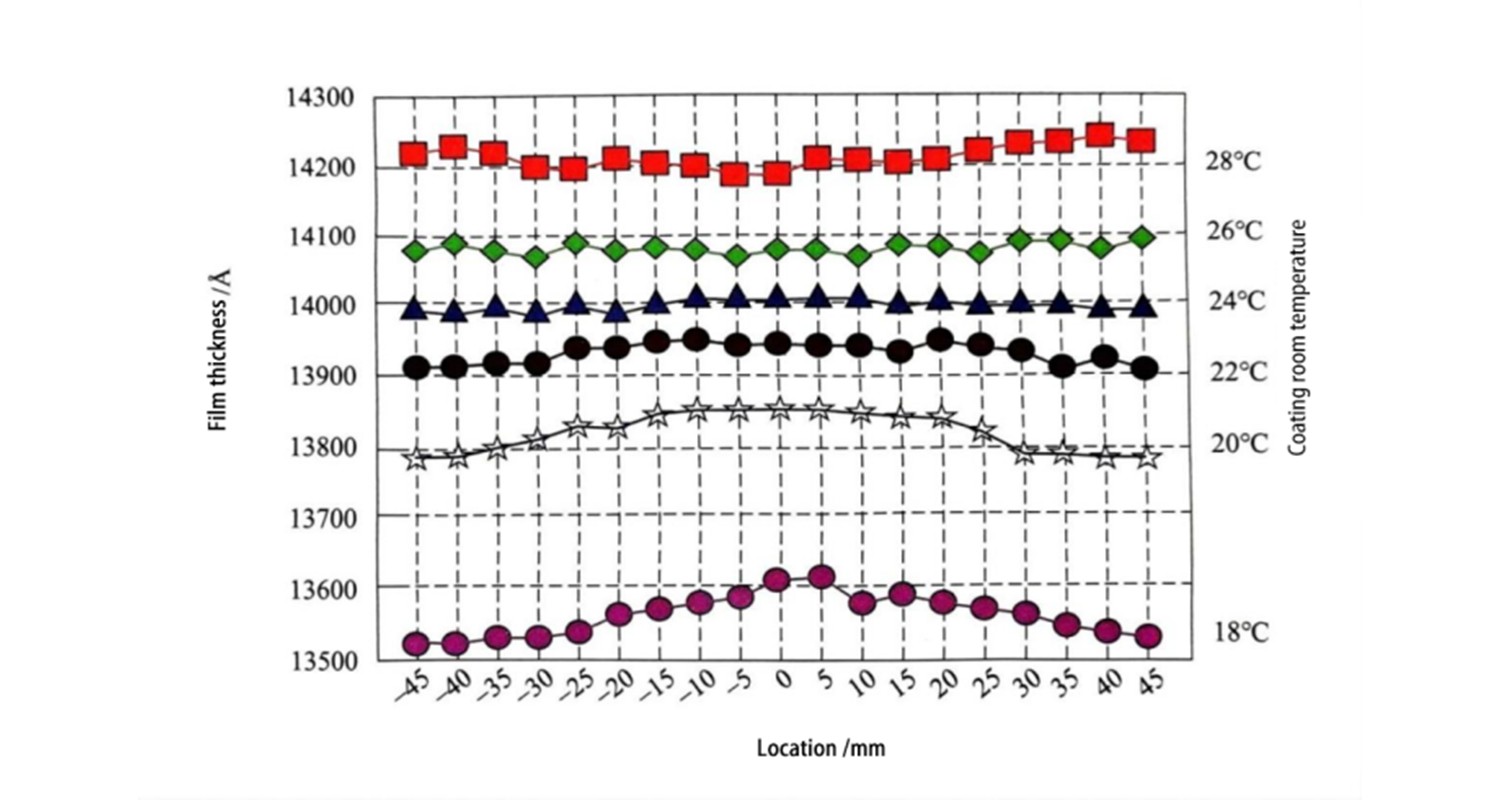
Рисунок 5: Зависимость между температурой и распределением толщины пленки во время нанесения покрытия.
Влияние скорости выхлопа во время нанесения покрытия
На рисунке 6 показана взаимосвязь между скоростью выхлопа и распределением толщины пленки. В отсутствие выхлопа видно, что центр пластины имеет тенденцию к утолщению. Увеличение скорости выхлопа улучшит однородность, но если ее увеличить слишком сильно, однородность ухудшится. Видно, что существует оптимальное значение скорости истечения.
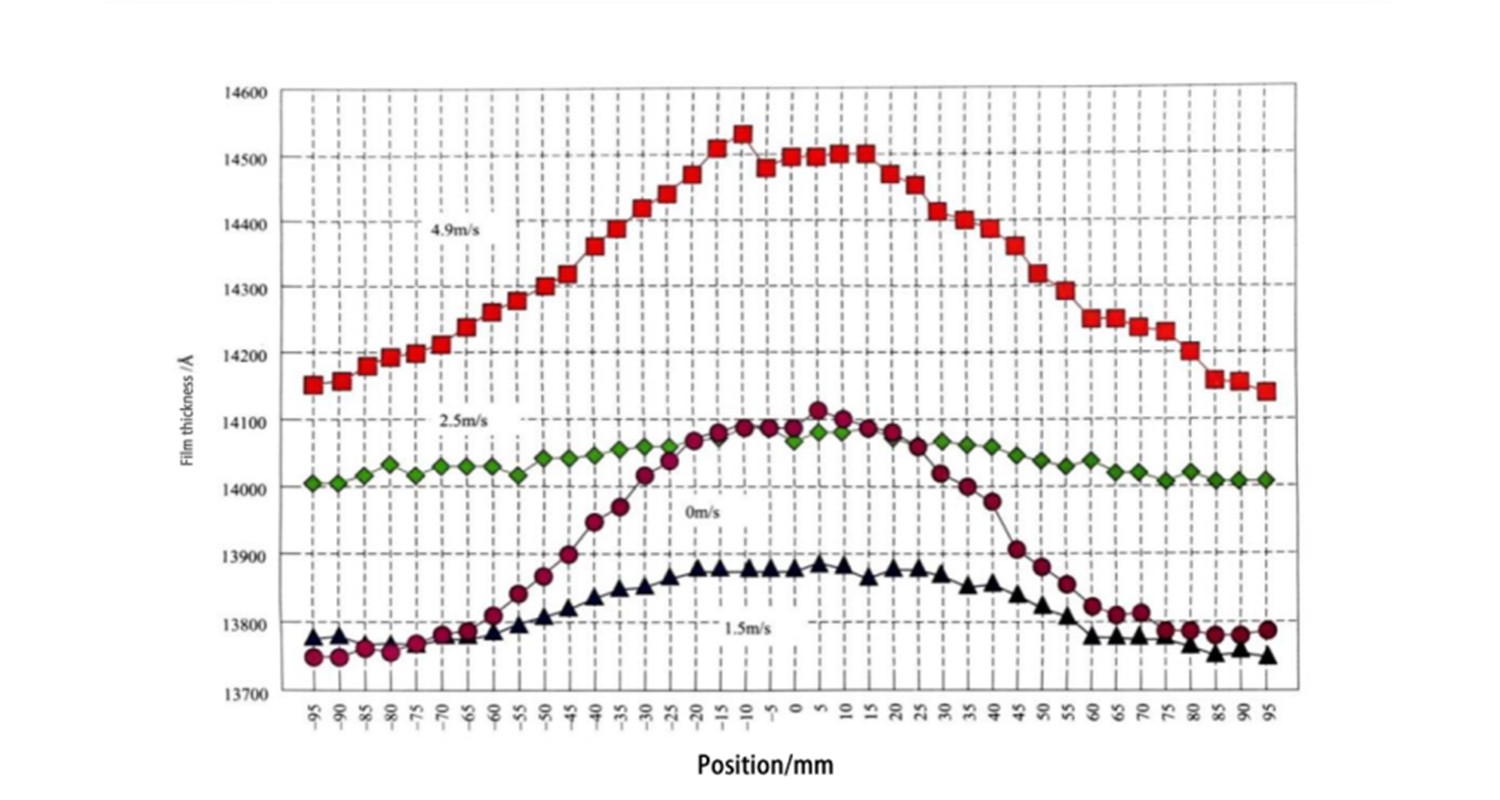
Рисунок 6: Зависимость между скоростью выхлопа и распределением толщины пленки.
лечение ГМДС
Чтобы сделать фоторезист более пригодным для нанесения покрытия, пластину необходимо обработать гексаметилдисилазаном (ГМДС). Особенно когда влага прикрепляется к поверхности пленки оксида кремния, образуется силанол, который снижает адгезию фоторезиста. Чтобы удалить влагу и разложить силанол, пластину обычно нагревают до 100–120°C и вводят туман HMDS, вызывающий химическую реакцию. Механизм реакции показан на рисунке 7. Благодаря обработке HMDS гидрофильная поверхность с малым углом смачивания становится гидрофобной поверхностью с большим углом смачивания. Нагревание пластины может обеспечить более высокую адгезию фоторезиста.
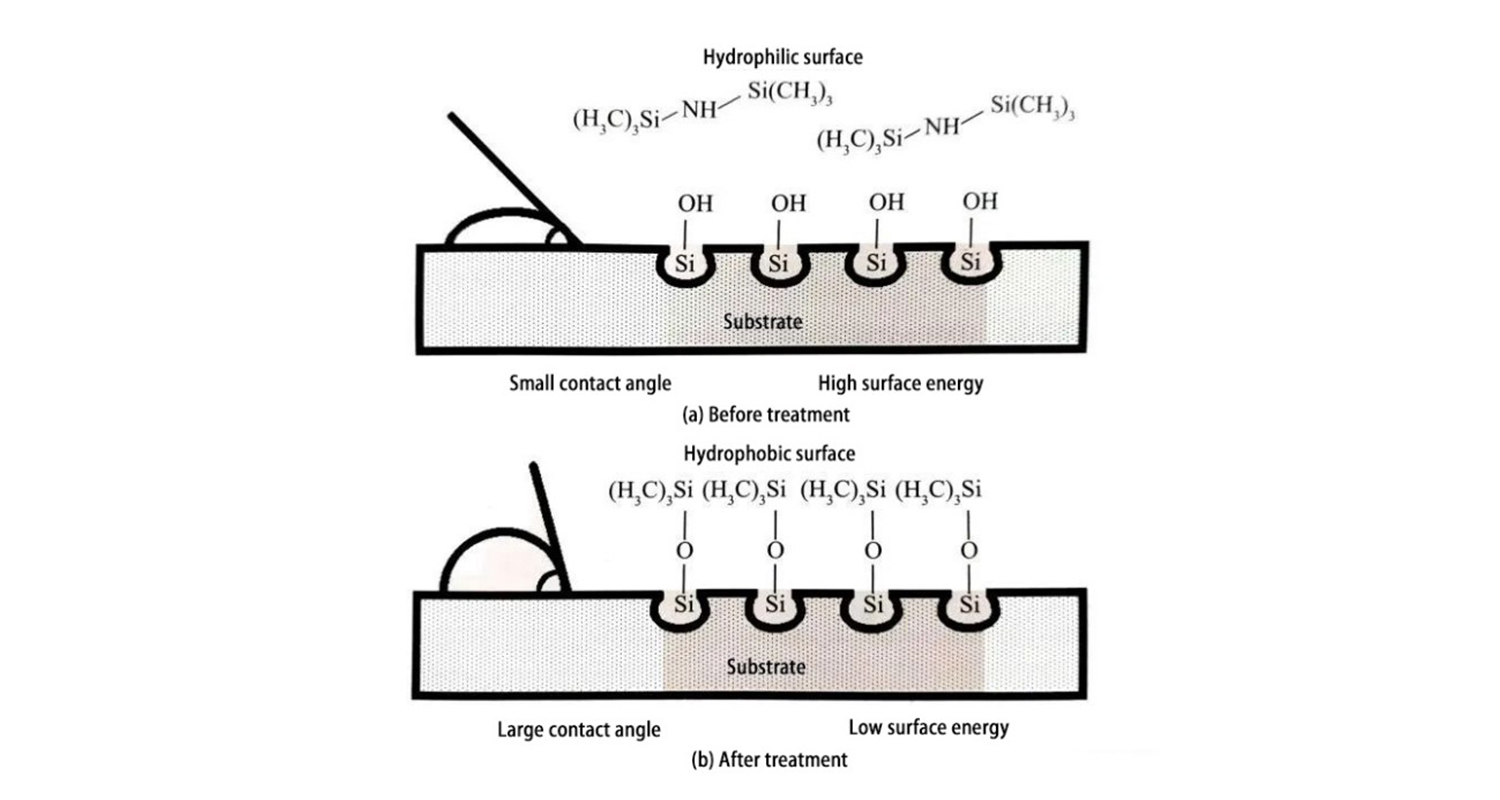
Рисунок 7: Механизм реакции ГМДС.
Эффект обработки HMDS можно наблюдать путем измерения угла смачивания. На рисунке 8 показана зависимость между временем обработки HMDS и углом смачивания (температура обработки 110°C). Подложка изготовлена из кремния, время обработки HMDS превышает 1 минуту, угол контакта превышает 80°, эффект обработки стабилен. На рисунке 9 показана зависимость между температурой обработки HMDS и углом смачивания (время обработки 60 с). Когда температура превышает 120 ℃, угол контакта уменьшается, что указывает на разложение ГМДС под воздействием тепла. Поэтому обработка HMDS обычно проводится при температуре 100-110 ℃.
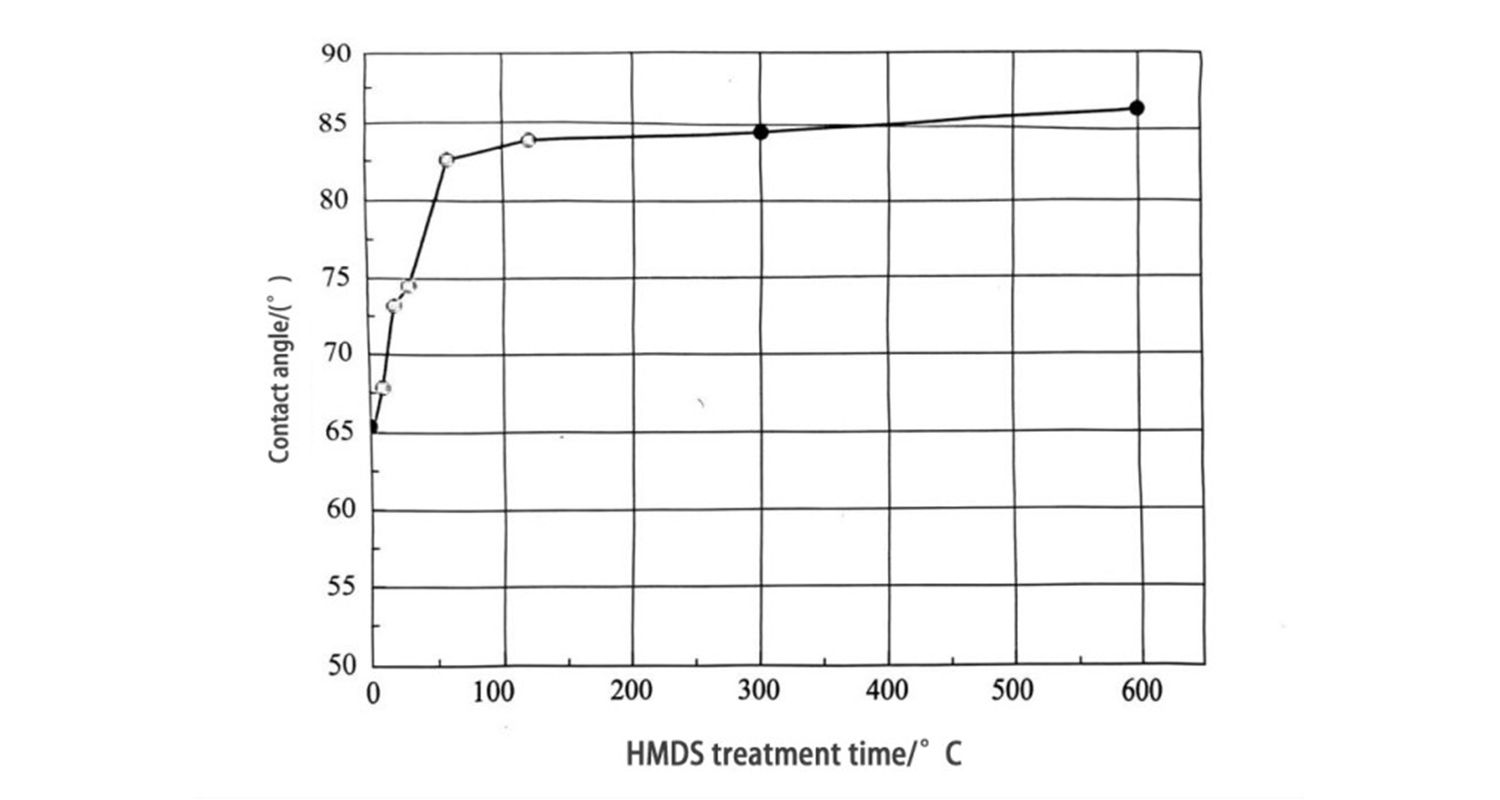
Рисунок 8: Взаимосвязь между временем лечения HMDS.
и угол контакта (температура обработки 110 ℃)
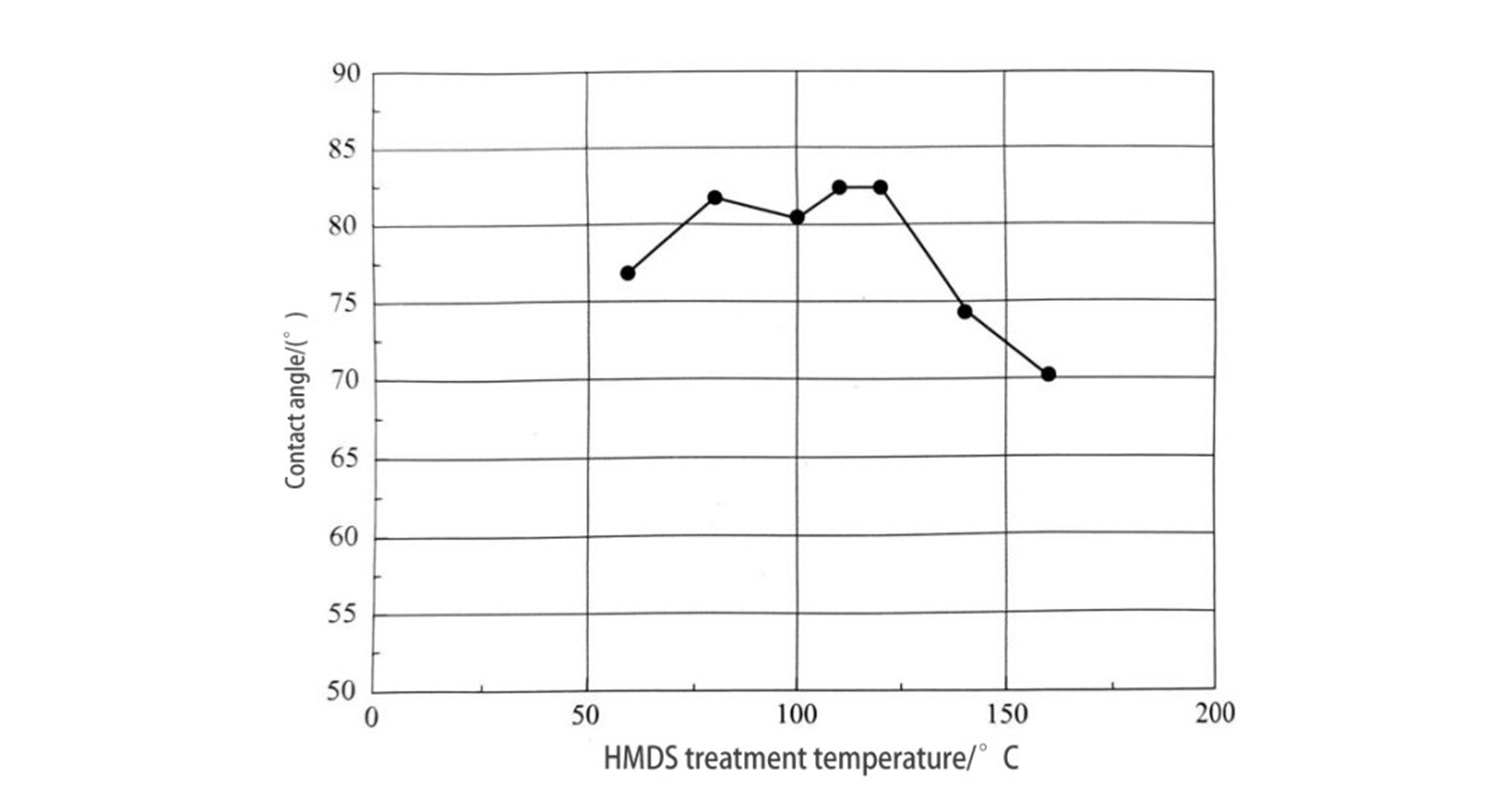
Рисунок 9: Зависимость между температурой обработки HMDS и углом контакта (время обработки 60 с)
Обработка HMDS проводится на кремниевой подложке с оксидной пленкой для формирования рисунка фоторезиста. Затем оксидную пленку травят плавиковой кислотой с добавлением буфера, и обнаруживается, что после обработки HMDS рисунок фоторезиста можно предотвратить от падения. На рисунке 10 показан эффект обработки HMDS (размер рисунка 1 мкм).
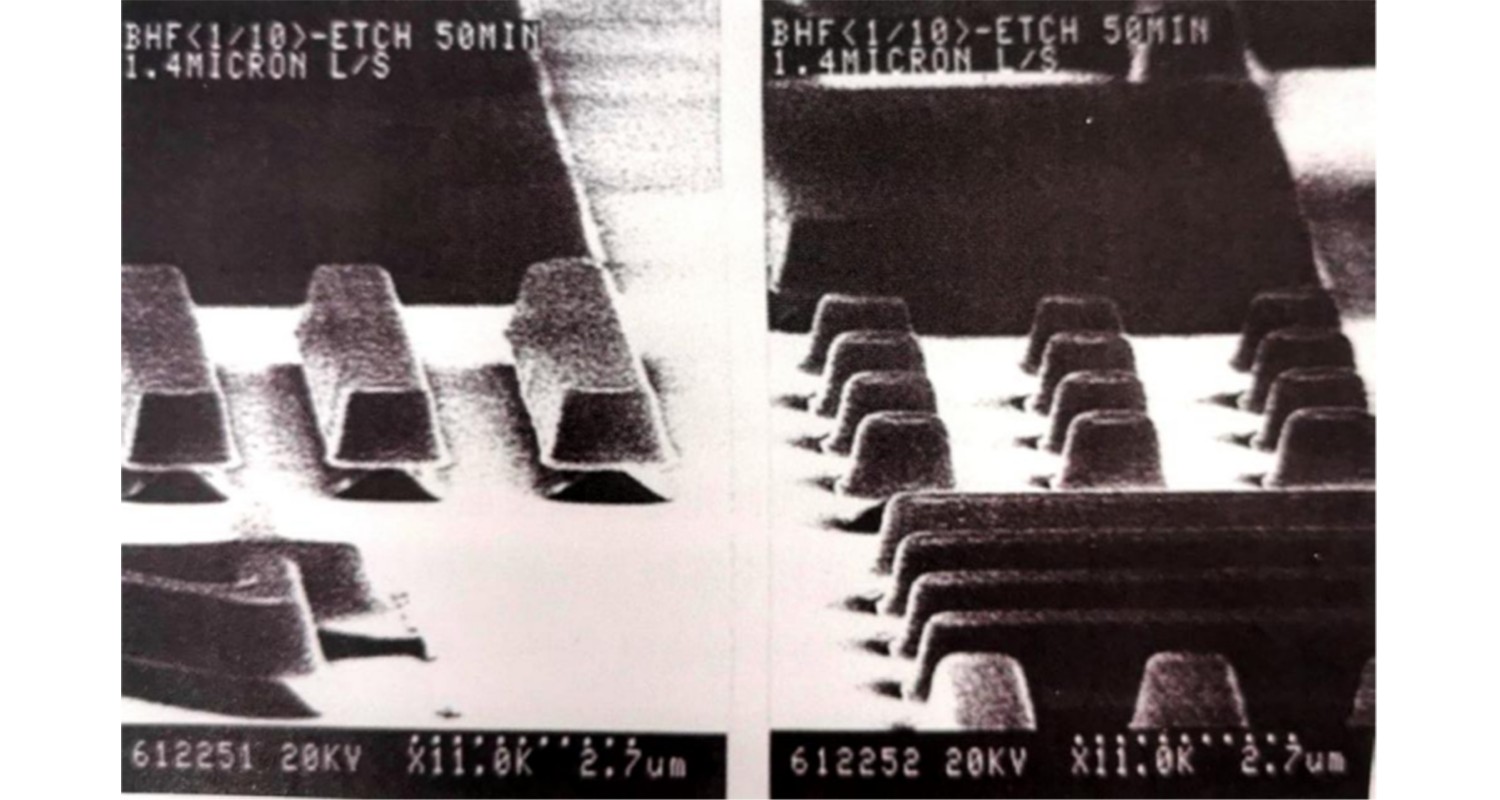
Рисунок 10: Эффект обработки HMDS (размер рисунка 1 мкм)
Предварительная выпечка
При одинаковой скорости вращения, чем выше температура предварительного обжига, тем меньше толщина пленки, что указывает на то, что чем выше температура предварительного обжига, тем больше растворителя испаряется, что приводит к уменьшению толщины пленки. На рисунке 11 показана взаимосвязь между температурой предварительной выпечки и параметром А Дилла. Параметр А указывает концентрацию светочувствительного агента. Как видно из рисунка, при повышении температуры предварительного обжига выше 140°С параметр А уменьшается, что указывает на то, что светочувствительный агент разлагается при температуре выше этой. На рисунке 12 показано спектральное пропускание при различных температурах предварительного обжига. При 160°С и 180°С увеличение коэффициента пропускания можно наблюдать в диапазоне длин волн 300-500 нм. Это подтверждает, что светочувствительный агент запекается и разлагается при высоких температурах. Температура предварительного обжига имеет оптимальное значение, которое определяется световыми характеристиками и чувствительностью.
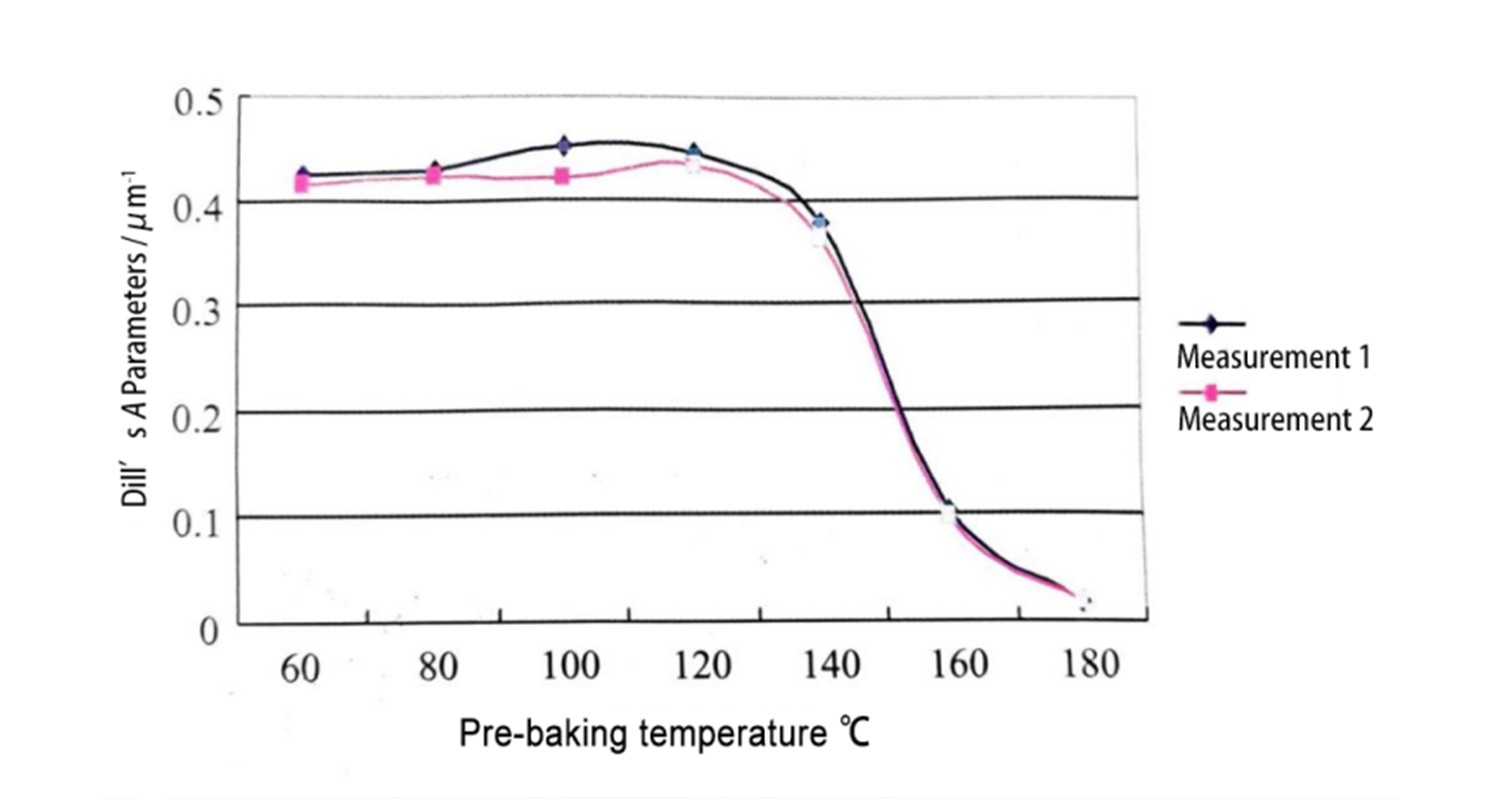
Рисунок 11: Зависимость между температурой перед выпеканием и параметром А Дилла.
(измеренное значение ОФПР-800/2)
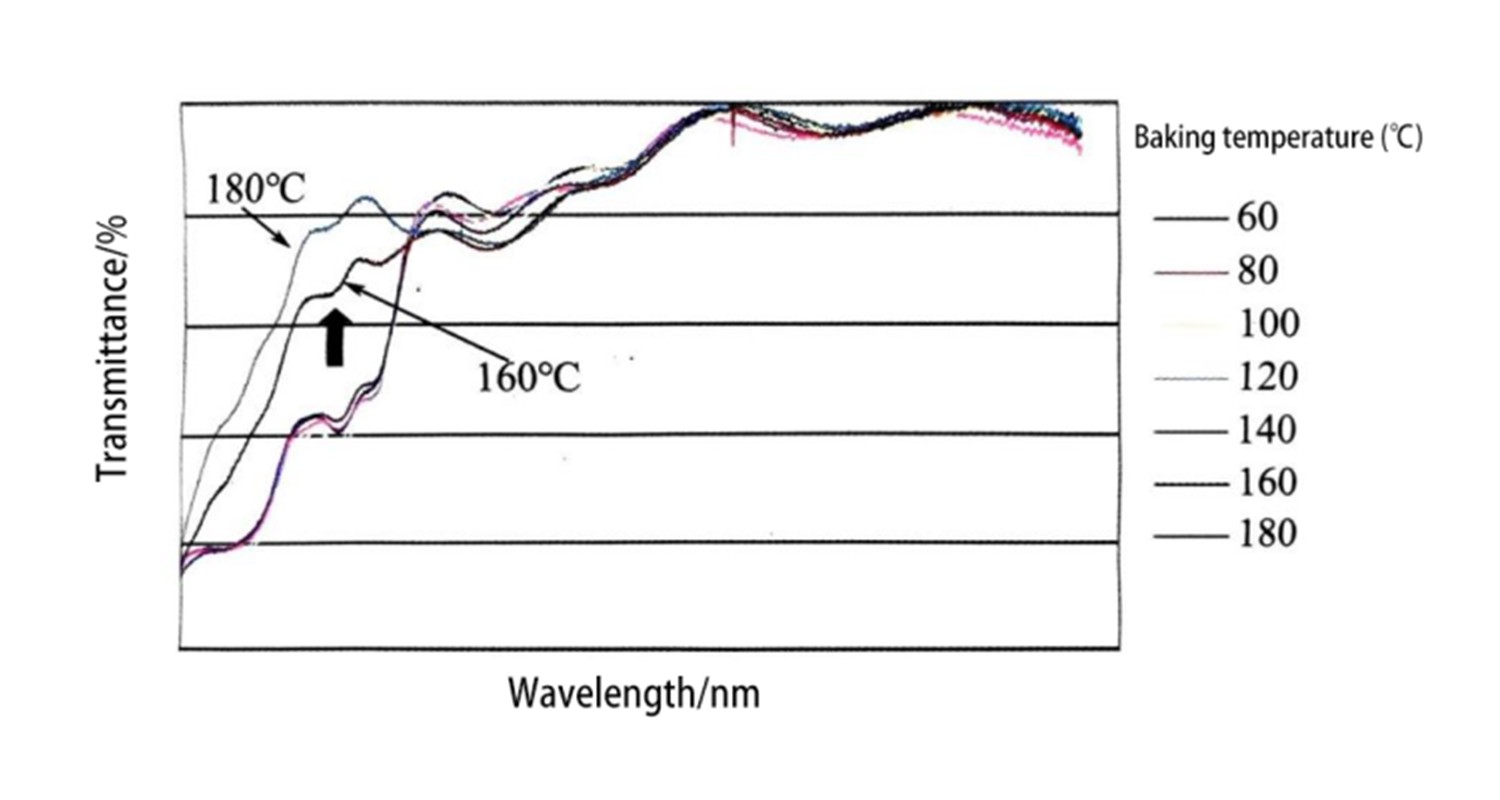
Рисунок 12: Спектральное пропускание при различных температурах перед обжигом.
(ОФПР-800, толщина пленки 1 мкм)
Короче говоря, метод центрифугирования имеет уникальные преимущества, такие как точный контроль толщины пленки, высокая себестоимость, мягкие условия процесса и простота эксплуатации, поэтому он оказывает значительное влияние на снижение загрязнения, экономию энергии и улучшение затрат. В последние годы центрифугированию уделяется все больше внимания, и его применение постепенно распространилось на различные области.
Время публикации: 27 ноября 2024 г.